Bearing rings within hydraulic systems must withstand intense pressures and transverse forces. They are used to protect the system’s metal components from rubbing against each other, and to keep the hydraulic force directed smoothly in the direction required.
The science of frictional force, and how to combat it, is known as tribology. Freudenberg Sealing Technologies (FST) has friction-fighting bearing rings made from a surprising number of materials, including PTFE, fibreglass and nylon.
Bearing rings in hydraulic cylinders
Hydraulic cylinders convert energy into force at the end of the hydraulic circuit. Transverse forces occur during the cycle, which must be absorbed by guide elements to keep the piston moving smoothly within the cylinder.
Bearing rings reduce friction between the metallic moving parts and absorb the transverse forces. While they can be made of metal, synthetic fabric materials are a cheaper, technologically advanced alternative.
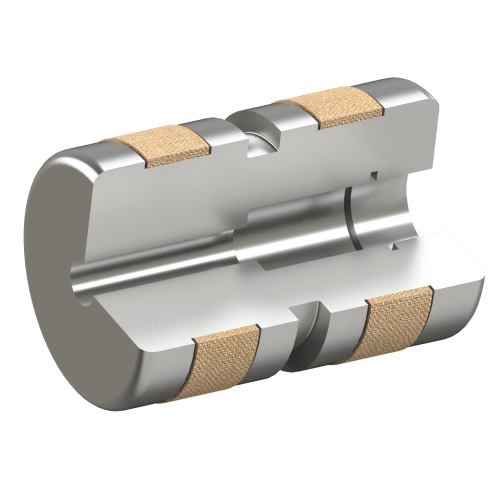
Hard fabrics make the difference
FST bearing ring materials contain fabric-based laminates, reinforced thermoplastics and PTFE (polytetrafluoroethylene). The fabric-based laminates, known as ‘hard fabrics’, include PTFE, nylon, glass-filled nylon, fibreglass and fabric-reinforced resin.
Bearing rings made from hard fabric are used in mobile hydraulics and heavy hydraulics, since they can endure high surface pressures. Adding PTFE to the material reduces the ‘stick-slip’ effect, the spontaneous stop-start jerking caused by friction.
The use of guide elements means there’s a low-friction, low-wear contact surface between the metal components of the hydraulic cylinder, minimising friction between the piston rod or piston body and the housing.
Bearing rings in context
When selecting guide materials for the cylinder, the operator must consider the requirement for load bearing capacity (pressure), tolerance play and cost restrictions. When choosing bearing rings, operators should consider:
- Specific load capacity;
- Thermal stability;
- Abrasion resistance;
- Impact to the counter surface;
- Elastic behaviour (mounting);
- Manufacturability (e.g. diameter range); and
- Compatibility with the used media.
Fabrics and surface pressure
For metal alloy bearing rings (copper-tin, copper-tin-lead bronze and copper-zinc) permissible surface pressure (dynamic) is in the range of 17 to 25 N/mm².
FST’s fabric-laminated bearing rings perform better than their metal counterparts under pressure. As a result of the low tension increase in the edge area and the elastic properties of these materials, a higher surface pressure is endured.
However, this pressure and temperature range varies greatly depending on the fabric-based laminated material used.
For more information about bearing rings, consult the FST catalogue which lists surface pressures and operating temperatures for each of its hydraulic system seals, or contact us.
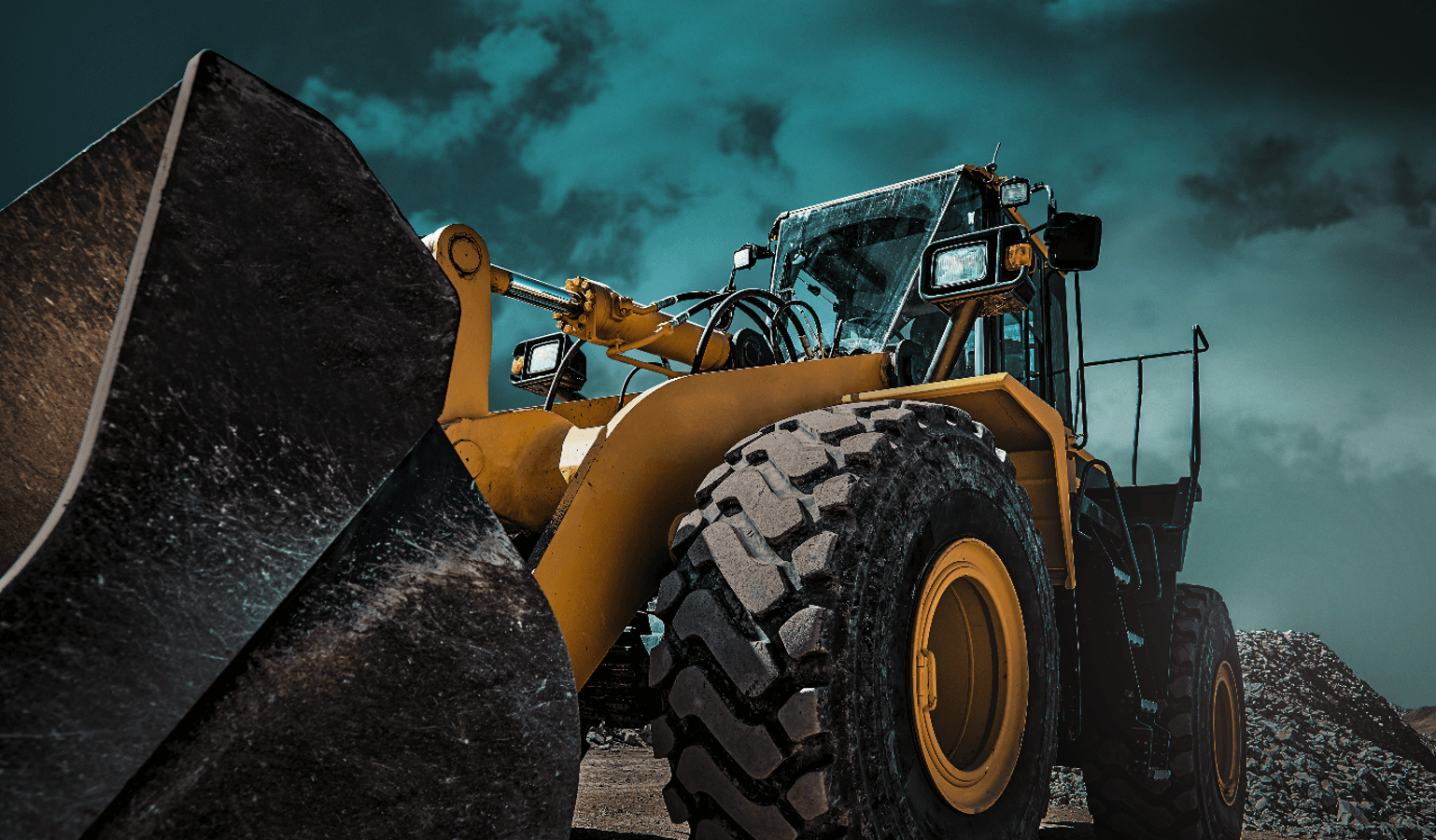