Whether it’s for pumps, wind turbines, excavators, beverage production lines or tunnelling machines, hydraulic seals need to work perfectly every time.
Seal leakage can be catastrophic financially as machinery experiences down time for repairs. It causes contamination to food and beverage production systems, and a failed seal in a mine operation can be potentially life-threatening.
Hydraulic seals should be tested under real time conditions to ensure they are fit for purpose, but what exactly are these real time conditions?
CIP/SIP testing for hydraulic seals
Testing hydraulic seals in real time means they have more chance of surviving in the field under intense pressure and continuous operation.
Automated CIP (Cleaning In Place) and SIP (Sterilisation In Place) are systems for cleaning and disinfecting production equipment without significant disassembly and assembly.
Freudenberg Sealing Technologies’ test plant allows tightness tests in CIP/SIP system media as well as steam and hot water under real conditions. This means information on seal performance can be obtained before serial use.
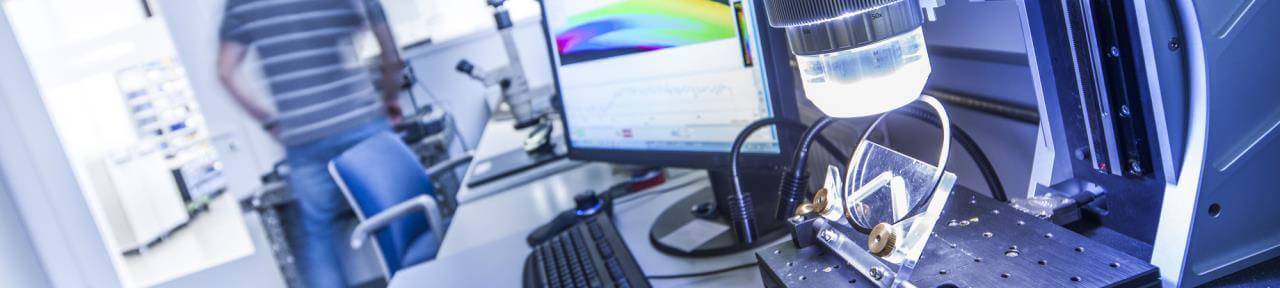
Cleaning media, maintenance and seal material
Matching the hydraulic seal material and its design to the system media and cleaning chemicals extends time between scheduled maintenance.
The range of CIP system cleaning media is wide and can include:
- Alkaline media: sodium hydroxide or potassium hydroxide based products;
- Acidic media based on mineral or organic acids; and
- Sodium hypochlorite based chlorine-alkaline media.
Cleaning temperature and potency of the media also affect the design of the seal and the material from which it should be made.
Test procedures and options
At Freudenberg, we don’t just design and produce seals, we test them too. When it comes to testing methods, we offer the following:
- Seal testing in connection with acids, alkaline solutions and disinfectants;
- Separate product infeed systems for valve and seal contamination;
- Testing critical applications with hot steam, cooling water and compressed air feed;
- Tests all kinds of seal in valves and accessories such as O-rings, membranes, lip and profile seals, moulded parts;
- Testing of seals in measuring devices and pumps; and
- Damage analyses.